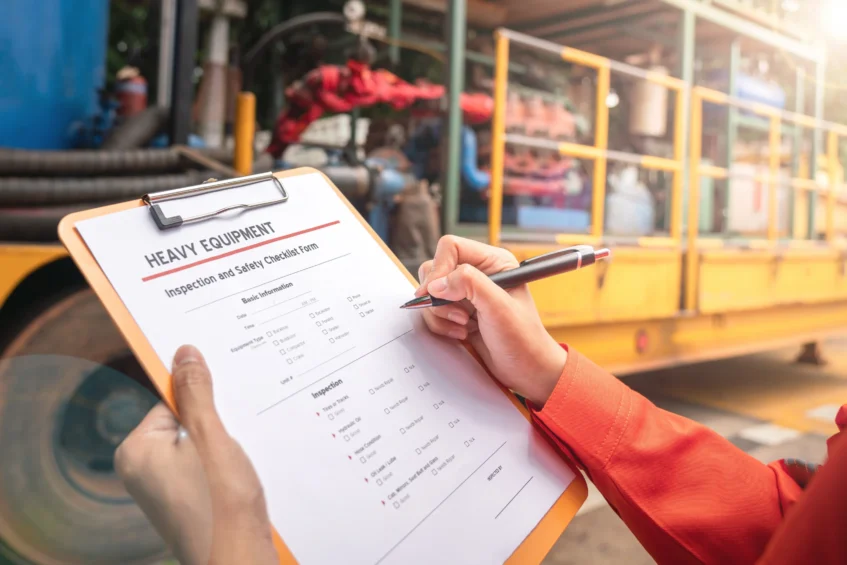
The industry of heavy machinery and construction has kept its safety requirements as a paramount attribute. One crucial aspect of maintaining a safe working environment is regular equipment inspections.
For that purpose regular Tool Inspection forms or an equipment training checklist may be utilized. These forms serve the purpose of supplying details for preventive maintenance, document inspection outcomes, and establish criteria for ensuring equipment is safely and appropriately maintained. In this guide, we will delve into the importance of equipment inspection forms, their components, and best practices for their implementation.
Advancing Equipment Inspections for Safety and Efficiency
Regular equipment inspections serve multiple purposes:
Safety Assurance
By conducting regular equipment inspections, potential hazards and malfunctions are swiftly identified, fostering a safer work environment and significantly reducing the risk of accidents and injuries on construction sites.
Operational Efficiency
Advanced inspection procedures and comprehensive maintenance protocols enhance the operational efficiency of heavy machinery, minimizing downtime and maximizing productivity, ultimately leading to smoother construction processes and project timelines.
Compliance
With Arrivy businesses can create tailored inspection digital forms, which can effortlessly help them meet safety regulations and industry standards, ensuring full compliance and mitigating the risk of penalties or legal issues associated with non-compliance.
Cost Savings
Through proactive monitoring and timely identification of issues, tools inspection checklists help prevent costly breakdowns and repairs, leading to substantial savings for businesses by reducing maintenance expenses and enhancing overall equipment longevity.
Components of a Good Equipment Inspection Form
An effective equipment inspection form should encompass various elements to ensure a thorough evaluation. Here are comprehensive key components that businesses can add to their Arrivy Equipment Inspection Forms:
Equipment Identification
Efficient equipment management begins with accurate identification and allows users to input crucial details such as equipment type, serial number, and location, streamlining inventory tracking and management processes.
With this information readily available, businesses can effectively monitor equipment utilization, schedule maintenance tasks, and allocate resources more efficiently.
Tailored Checklist
It is crucial to understand that different industries and equipment types have unique requirements. Therefore, the platform offers customizable checklists tailored to specific industry standards and equipment specifications.
Whether it’s construction vehicles, manufacturing machinery, or warehouse equipment, users can create comprehensive checklists covering critical aspects of equipment condition, safety features, and operational parameters.
This tailored approach ensures that inspections are thorough and relevant to the equipment being evaluated, enhancing overall effectiveness.
Visual Inspection
Visual inspection is a fundamental aspect of equipment maintenance and safety assessment. A user-friendly interface enables technicians to conduct visual inspections efficiently, capturing digital images and notes to document any visible damage, leaks, or signs of wear and tear.
By integrating visual inspection capabilities into the inspection process and forms, businesses can quickly identify potential issues, enabling them to take proactive maintenance actions.
Functional Checks
Beyond visual assessment, Arrivy empowers technicians to perform functional checks on critical equipment components with ease. Users can evaluate the functionality of brakes, hydraulics, safety features, and other essential systems by systematically recording these components within their Arrivy digital form. Furthermore, businesses can ensure that equipment operates safely and reliably and minimize the risk of unexpected failures and downtime.
Detailed Documentation
Effective documentation is essential for tracking inspection findings, documenting defects or deficiencies, and facilitating follow-up actions. A good checklists enables users to record detailed observations directly within the inspection form, including notes, images, and audio recordings. This comprehensive documentation provides a clear record of equipment condition and inspection outcomes, empowering businesses to make informed decisions regarding maintenance prioritization, repair scheduling, and resource allocation.
Signature and Date
Accountability and compliance are crucial aspects of equipment inspection and maintenance processes. This ensures that inspections are properly documented and validated, establishing a clear audit trail of compliance with regulatory requirements and internal quality standards.
Advanced Practices for Equipment Inspection
Implementing effective equipment inspection procedures involves adhering to best practices:
Regular Frequency
Inspections should be conducted at regular intervals based on manufacturer recommendations, usage frequency, and regulatory requirements to ensure equipment reliability and safety.
By adhering to a structured inspection schedule, potential issues can be identified early, minimizing the risk of unexpected failures and optimizing equipment performance over time.
Training
Proper training of personnel responsible for conducting inspections is essential for maintaining high standards of thoroughness and accuracy. Investing in comprehensive training programs equips inspectors with the necessary knowledge and skills to effectively evaluate equipment condition, identify potential hazards, and adhere to inspection protocols.
Additionally, ongoing training initiatives ensure that inspectors stay updated on industry best practices and emerging technologies, enhancing the overall effectiveness of the inspection process.
Documentation
Effective documentation practices are critical for tracking inspection findings, documenting corrective actions, and maintaining compliance records. Implementing digital documentation systems allows for centralized storage and easy access to inspection forms, reports, and maintenance records.
By maintaining organized and detailed documentation, businesses can demonstrate regulatory compliance, track equipment history, and facilitate data-driven decision-making to optimize maintenance strategies.
Continuous Improvement
Continuous improvement is key to enhancing the effectiveness of equipment inspection procedures over time. Periodically reviewing and updating inspection protocols enables businesses to incorporate feedback from inspectors, address emerging risks, and identify opportunities for optimization.
By leveraging data analytics and performance metrics, organizations can identify trends, prioritize areas for improvement, and implement proactive measures to enhance equipment safety and reliability.
Collaboration
Foster collaboration between maintenance teams, operators, and safety personnel to ensure a holistic approach to equipment safety and maintenance.
Encouraging open communication and sharing of insights allows stakeholders to collaborate effectively in identifying potential risks, implementing preventive measures, and addressing maintenance issues in a timely manner.
By fostering a culture of collaboration, businesses can leverage collective expertise and resources to optimize equipment performance and enhance overall workplace safety.
Conclusion
A comprehensive approach to equipment inspections revolutionizes safety and efficiency in heavy machinery and construction industries. By integrating regular inspections, tailored checklists, advanced visual and functional checks, and detailed documentation within its platform, tools like Arrivy can help businesses ensure not only the safety of their workers but also contribute to the longevity and operational efficiency of their machinery.
Furthermore, implementing best practices and fostering collaboration further enhances the effectiveness of equipment inspection processes, allowing businesses to mitigate risks, comply with regulations, and achieve cost savings through proactive maintenance. Businesses can elevate their equipment inspections to new heights, ensuring a safer and more productive work environment.