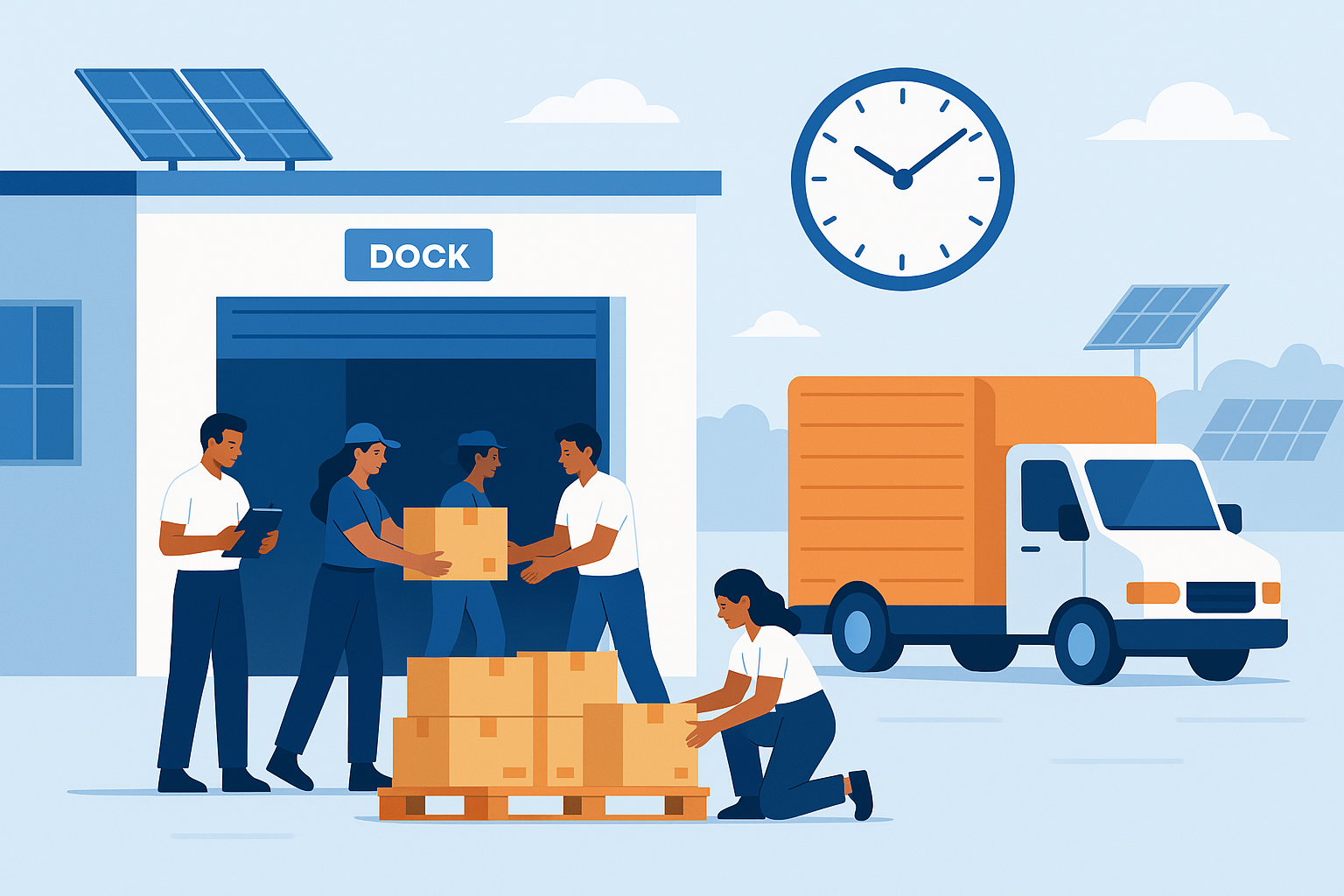
Careful administration of your outbound logistics is important, and the need to optimize these processes has never been more pressing. A whopping 79% of surveyed companies say that optimizing outbound docks as part of the supply chain improved their revenue significantly (G2Crowd, 2023).
For all the businesses stuck in manual mode, completing one process takes around 24-48 hours due to shipment delays, inventory discrepancies, and high return rates. Meanwhile, successful companies zip through this process in just 2-6 hours, which is 4 to 8 times faster and efficient (F.CBCo, 2024). In this blog, you will learn how you can optimize this process for faster outbound dock fulfillment.
Key Takeaways
✓ What is Outbound Dock Management?
✓ How to Optimize and Improve Outbound Fulfillment?
✓ Modern Outbound Strategies to enhance workflows
✓ How to Measure Metrics to Stay Ahead?
What is Outbound Dock Management?
Before we discuss optimization, we need to have a clear understanding of the process companies employ to ship docks fast, accurately, and on time. Outbound dock management is all about organizing and managing the shipment of goods from a warehouse to their final destinations, whether that’s customers, retailers, or other locations.
The process of outbound dock management involves:
- Sales Order Processing (SOP)
- Picking and Packing of Products
- Lane Staging and Transportation Planning
- Loading and Documentation
- Goods Tracking
How to Optimize Outbound Dock Management to Improve Workflows?
Adjusting your dock management to operate at peak performance will help you improve workflows. “Dock optimization is about making dock management processes more efficient”. The main objectives for optimizing docks are to:
- Eliminate cash leaks
- Increase product quality
- Distribute goods efficiently
- Control Turnaround times
- Save from detention fees
- Respond with agility to changing market and economic conditions
1- Sales Order Flow in the Warehouse
After the complete inbound process, the outbound warehouse sales workflow starts with a purchase order (PO). Signaling the warehouse team to indicate which items are ready for picking and packing within the facility. This triggers a series of actions, including
- Mapping items for Instant Location Tracking
- Ensure item quality with instant verification tools
- Effortless Inventory Allocation for Optimized Operations
- Simplify documentation preparation
- Leverage field dispatch software to automate product mapping, quality checks, and inventory tasks
In most cases, employing an efficient order management system can ensure accuracy and minimize delays, creating a positive, error-free customer experience. After an order is processed, warehouse staff carefully pick the correct items from inventory.
This involves preparing them for shipment with the right dunnage and labels. Then these picked items are moved to staging lanes (designated areas next to the dock doors). These staging lanes act like a transitional checkpoint for orders, where everything gets verified for reiteration.
The staging area should always be close to the picking area, clearly marked, and kept clear of excess inventory or equipment at all times, ensuring it is available for use in the inventory receiving process.
2- Classifying Warehouse Locators
When items are defined in specific areas within the warehouse, you can improve the organization of outbound dock management in a snap. Here are some places to define or mark before outbound logistics.
- Stock Locator → Where inventory is stored.
- Dock Door → Where trucks load/unload.
- Staging Lane → Temporary holding before shipment.
Companies lose over $25,000 per dock door each year due to inefficient or disorganized dock operations (Burton, 2023). Optimize flow between loading bays and temporary storage with organized allocation that preserves operational agility.
Stock Locator
These are designated areas within the warehouse for systematic inventory storage before order fulfillment. You can optimize and improve the workflow of this storage zone by following
- Utilize proximity-based slotting to position high-demand SKUs closer to staging lanes to minimize travel time.
- Start processes automated location tracking with Warehouse Management Systems (WMS) and RFID/barcode scanning to optimize inventory placement.
- Implement dynamic replenishment, which involves real-time stock monitoring to prevent shortages and overstocking.
Dock Door
These are gateways used for loading and unloading docks. Without an optimized dock schedule, trucks arrive unpredictably, creating long queues outside the warehouse. For example, if orders aren’t ready on time, trucks wait longer. 40% of delayed appointments face over 2 hours of detention, costing $50-$100 per incident (Optym, 2024), leading to:
- Missed delivery windows (increased carrier detention fees).
- Frustrated drivers may refuse future shipments due to long wait times.
- Slow down the entire supply chain.
In this case, you can utilize automated dock scheduling software for slot management to prevent congestion and turnaround times. Dock scheduling software has proven to improve truck turnaround times by 70% (Gowans, 2023). Trucks and shipments must be scheduled in advance according to the availability of dock doors.
Dock doors are assigned based on
✓ Shipment type
✓ Staging lane availability
✓ Truck size
This can be managed manually or through warehouse management systems. Goods should be staged in designated lanes near the dock doors before loading. Trucks are positioned securely at the dock door using dock levelers or shelters to create a seamless connection between the truck and the warehouse.
Workers or automated systems transfer goods from staging lanes into trucks. Proper equipment, like forklifts, pallet jacks, or conveyor systems, is used to maximize efficiency. Goods are inspected for damage, and all necessary documentation (e.g., bills of lading) is completed before dispatch.
Staging Lane
Temporary zones for consolidated shipments before loading onto outbound vehicles. You can optimize this strategic allocation. Align staging lanes with dock doors based on shipment volume and priority. Use RFID and barcode verification to ensure correct orders are staged for departure. By systematically optimizing these warehouse locators, organizations can enhance outbound logistics, reduce operational bottlenecks, and accelerate order fulfillment.
3- Optimizing Dock Scheduling and Trip Planning
Without automated systems, managers lack real-time visibility into dock operations, making it difficult to coordinate activities and respond to changes.
Streamlined dock scheduling is vital for operational efficiency:
- Assign specific dock doors for each outbound trip to direct trucks accurately.
- During the pick release process, utilize systems that automatically suggest staging lanes based on dock appointment details.
- If no specific staging lane is assigned, default settings act as a fallback.
Outbound Dock Management Process Improvement Strategies:
1. Cross-Docking Strategies
What is Cross-Docking?
To improve your outbound docking, you can employ cross-docking, which is a logistics strategy where incoming shipments are unloaded from inbound trucks and directly transferred to outbound trucks with little to no storage time. This reduces warehouse space usage to accelerate product movement.
How Does Cross-Docking Work?
✓ Inbound shipment arrives at the warehouse from suppliers or manufacturers.
✓ Items are quickly sorted and allocated based on their destination.
✓ Instead of storing products in inventory, they are moved directly to staging lanes assigned to outbound shipments.
✓ Goods are loaded onto outbound trucks for final delivery.
Benefits:
- Cross-docking reduces the need for long-term inventory storage.
- Products move quickly through the supply chain, improving delivery times.
- Less movement means lower labor expenses and fewer handling errors.
- Ensures fast turnover for products like food, pharmaceuticals, and time-sensitive shipments.
Walmart employs cross-docking to consolidate shipments from multiple suppliers into full truckloads. This approach reduces distribution costs and improves supply chain efficiency, enabling faster replenishment of stores.
2. Lean Principles in Outbound Dock Management
What is Lean Logistics?
Lean logistics focuses on eliminating waste and optimizing workflows at every stage of warehouse operations. This includes 5S Methodology (Sort, Set in Order, Shine, Standardize, Sustain). Organizes staging lanes for easy access.
How to Apply Lean Principles?
✓ Identify waste (Muda) to analyze outbound dock operations like unnecessary handling, idle time, and excess inventory.
✓ Establish clear dock schedules, assign staging lanes systematically, and ensure optimized loading sequences.
✓ Maintain a steady movement of goods by reducing bottlenecks at dock doors.
✓ Ensure dock doors and staging lanes are strategically placed to minimize travel distance for warehouse personnel.
✓ Use Visual Management Tools such as digital dashboards, signage, and real-time tracking to improve dock visibility and coordination.
✓ Adopt a culture of continuous improvement (Kaizen) to regularly review dock performance metrics and refine processes based on data insights.
Benefits:
- Reduces excess movement, waiting time, and resource misallocation.
- Standardized workflows enable faster, smoother dock operations.
- Lean strategies minimize labor expenses and operational inefficiencies.
3. Just-In-Time (JIT) Workflows
What is JIT in Logistics?
Staging areas overflow with unsorted shipments, delaying loading and causing mix-ups. Just-In-Time (JIT) logistics ensures that materials and products arrive exactly when they are needed for shipment, reducing excess inventory and storage costs.
How does JIT Works?
✓ Demand forecasting to predict shipment needs.
✓ Work closely with suppliers and carriers to schedule deliveries aligned with outbound shipment schedules.
✓ Track inventory levels dynamically to prevent overstocking or shortages.
✓ Dock Scheduling to align inbound shipments with outbound truck departures to minimize dwell time.
✓ Use of warehouse management software (WMS) to adjust schedules and reroute shipments as needed.
Benefits:
- Products arrive just in time for shipment, eliminating excess stock.
- Less storage means more efficient space utilization.
- Enhances supply chain agility.
- Less capital is tied up in stored goods, improving financial flexibility.
Introduce Key Performance Indicators (KPIs) into Your Workflow:
Keeping your outbound dock management in track can level up supply chain performance.
- Measure dock turnaround time on how quickly a dock can be cleared for the next shipment.
- Track how accurately loads are assembled to minimize errors and rework.
- Monitor carrier wait times and reduce the amount of time carriers wait at the dock, ensuring smoother operations.
Conclusion
Timely outbound processes, driven by efficient order flow, can improve customer satisfaction scores by up to 15%. Optimizing your outbound dock management delivers both time and cost savings. Implement these strategies to advance toward operational excellence.
What’s the next-generation solution?
Are your docks never on time? Are your outbound shipments dealing with congestion? Then, a robust dock scheduling software can help you. A solution designed to pull you out of poor scheduling by streamlining operations and improving real-time coordination. Whether you are dealing with multiple warehouses or in need of digital documentation, Book a demo today!